The oil and gas industry is the lifeblood and oxygen of the modern world. It produces the stuff that powers the power stations, providing the energy on which we all depend if we live in a country with even a moderate infrastructure.
Much as we’d all like to live on fresh air, and run our iMachines on the light that shines in through our windows, the harsh reality is that the dirty and dangerous business of fossil fuels is still the biggest generator of energy in the world today.
No developed or developing economy on Earth can do without oil and gas, and no oil and gas plant can do without systems to prevent any downtime. Every second of unscheduled downtime can cost the oil and gas company millions of dollars. Not only that, the secondary effects on all the businesses connected to the oil and gas company’s supply lines – which basically permeate the whole of society – could be devastating to a nation’s economy and wellbeing if those seconds turn into minutes, hours or days.
Certainly there are plenty of films and other works of fiction which have imagined a dystopian world in which there’s no energy and no electricity; no fuel, therefore no real society, with civilisation just about surviving.
It follows then that keeping the heart of the oil and gas pumping is critical not just to the energy companies, it’s also pretty important to everyone else.
Field of streams
The oil and gas industry is divided into three major sectors: upstream, midstream and downstream.
- Upstream includes such activities as exploration and extraction, operational gas and oil fields, and the companies therein.
- Midstream can include some elements of upstream as well as downstream, but perhaps can be most simply thought of as the logistics bit – the storage and transportation of the oil and gas, either through pipelines, or land, sea and air transportation;
- Downstream can also be considered the refining part – the bit where the oil and gas into turned into finished products, such as gasoline, jet fuel, heating oil, and hundreds of other petrochemicals.
The data network
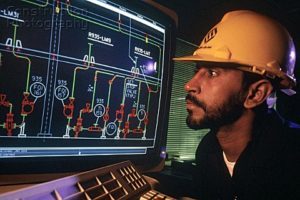
Oil refinery control room in Saudi Arabia, running Honeywell UOP systems
In order to keep the wheels turning, or oil flowing, or gas circulating, without interruption and the dreaded unscheduled downtime, oil and gas companies use a massive number of sensors all over their plants and operations. These sensors are connected to a central database which can visualise the information on screens for plant and process managers to monitor.
If the managers see there is a problem somewhere, they can take action and remedy the situation as fast as possible. What’s even better is if managers can predict there may be a problem in the future and take pre-emptive action: any leaks can be plugged before they get too big and cause colossal damage; and any worn-out bits of equipment can be replaced before their tottering eventually becomes a crash not just for the machinery itself, but all the other things connected to it.
These are some of the features and benefits of connectivity, often referred to in the world of business as the Internet of Things. There’s also the Industrial Internet of Things, which features special types of Ethernet networking and other technologies specific to industry. And if the IoT or IIoT can be thought of as the new pipeline or transportation network, the data which flashes through it at the speed of light can be considered to the be the fuel, or even food for thought.
Prospecting for patents

A Petrovietnam facility
Arguably, the company which knows the most about all this oil and gas business is UOP, which may be a part of Honeywell now, but was originally a company on its own, having been founded in 1914 to commercialise 12 inventions by Jesse Adams Dubbs, who believed in the business so much he called his son Carbide.
After many years of operation in co-operation and in competition with other supermassive black gold prospectors and other types of companies which grew to take over the world over the intervening decades, UOP was eventually acquired by Honeywell in 2005 for a total of around $2 billion.
Today, Honeywell employs 130,000 people and has annual revenues of approximately $40 billion a year and UOP represents a significant and growing portion of this. And UOP, with 5,000 staff in 30 locations, is still among the world’s leading inventors of technological processes, filing hundreds of patents a year.
In 2015, Honeywell UOP filed for and won 671 patents – a record for the company. Around half of those patents are in the US, and most of them relate to inventions which more efficiently convert hydrocarbons into transportation fuels and petrochemical products, making better use of the petroleum and natural gas feedstocks while consuming less energy, according to the company.
So, cars and other transportation will be cleaner as a result.
Not too much data
All of this research by UOP generates a lot of data, and when added to the data the company collects for and on behalf of its clients, Honeywell UOP could be regarded as a “Big Data” company, especially as it was until relatively recently engaged in a $250 million, 10-year alliance with Big Blue, or IBM, which is definitely a big data company.
The Honeywell IBM alliance resulted in the development of enterprise resource planning software and manufacturing execution systems – cloud platforms for business. And given the exponential increase in demand for data in all walks of life, UOP’s IIoT-based, data-driven services, are likely to become central to the industrial giant’s business going forward.
One of the men responsible for all the data and analytics systems at Honeywell UOP is Zak Alzein, whose full title is vice president and general manager of Connected Performance Services, or CPS, at UOP.
CPS is a newly created entity, launched by Honeywell a couple of months ago. It’s one of many industrial cloud, or industrial internet, platforms to have emerged in the past couple of years, although this one has a company with more than 100 years of history behind it.
Honeywell UOP’s CPS platform is used in a wide range of industries, including logistics, building management, retail, aerospace, smart electricity grids, and, perhaps most importantly because of the company’s history, the oil and gas industry.
Alzein was involved in the recent UOP deal with Petrovietnam, in which the company is contracted to provide its IIoT-based CPS system to manage and improve Petrovietnam subsidiary Binh Son Refining and Petrochemical’s manufacturing operations in Quang Ngai City, in Vietnam.
In an exclusive interview with Robotics and Automation News, Alzein provided some insight into UOP’s connectivity services, which while mainly geared to the petrochemicals sector, have capabilities relevant to other manufacturing sectors.
Time is priceless
Manufacturing is often divided into two broad categories:
- discrete manufacturing, which is the production of finished products, such as smartphones, cars and so on; and
- continuous manufacturing, which is mainly concerned with the production of materials, such as oils and gases which can be used by the discrete manufacturers as raw materials for their goods or as fuel for their factories.

Zak Alzein, general manager, UOP Connected Performance Services
Alzein says: “If we talk about continuous manufacturing, there is certainly a lot of different industries in this category, and oil and gas is one of those. This is where I am focused, and it’s where I do a lot of work – upstream, midstream and downstream, including petrochemicals, chemicals, the pharmaceutical industry, and so on.
“There are common things between all of them: obviously, considerations about efficiency and productivity. A common question might be, ‘How do I increase my output from the facilities for my input?’
“You’ll find this in crude oil, petrochemicals, or anywhere else. It might be considerations about energy efficiency, or output, or different aspects of input. So, how do I get more output for my input?
“And that is a function of a number of things. One big aspect that we deal with in these industries is plant reliability. The minute you have disruption to your manufacturing operation is a minute that can cost a lot of money. Whether you’re a discrete manufacturer or in continuous manufacturing, and whether it’s your equipment or your processes, any unplanned downtime – with things breaking down or not working reliably – production time goes down and costs go up.
“This is the area we pay a lot of attention to. How do I maximise utilisation? How do I maintain production?
“For example, a very well-run refinery might be at 93 to 95 per cent utilisation, so that’s a refinery that’s running very hard. A petrochemical plant, if you’re running in the low 90s, you’re doing very well, and some of that is due to planned downtime, some of it is due to unplanned downtime.
“So, you might have 1, 2, 3 per cent flawed production because of problems related to equipment reliability.
“In some processes that are also very difficult and cumbersome, you might even have 10, or more than 10 per cent downtime impact, which could be significant. Depending on the size of that manufacturing facility, you’re dealing with millions or even tens of millions dollars’ equivalent in lost production.”
Critical juncture

UOP researchers at one of the company’s labs
Alzein goes on: “I’ll give you an example. Sometimes, if a piece of equipment – a very critical piece of equipment – shuts down in a refinery, it might lead to serious consequences.
“A refinery might have 20 to 30 major power efficient units, and a handful of those are considered the heart of the refinery, and when those go down, it would cause the whole refinery to go down. And if the whole refinery goes down, it takes you a minimum of a week, sometimes more, to bring it back up.
“You need a refinery to run all the time. Even when they have some downtime with some equipment, it may not take a whole refinery down. It may take some sub-units down, but not the whole refinery.
“A related issue to consider is to do with maintenance. A lot of times you do maintenance on equipment on a certain timeline or in a certain rotation, and sometimes that isn’t necessarily the optimum way because you could be doing maintenance and spending money on pieces of equipment that do not necessarily merit the resource allocation.
“In the meantime, you could have other pieces of equipment which may be close to breaking point and losing them may cause a larger production loss.
“Also, maintenance and reliability increasingly involves predicting what work needs to be done with which pieces of equipment, checking their health and taking care of them, and in what order.”
Energy efficiency is the key
Like a top Olympic athlete, when you’re a top-tier company, every fraction of a second’s worth of optimisation can lead to momentous advantages in the ongoing race that is continuous manufacturing.
But whether you run a petrochemical plant, or just run your central heating system at home, one of the most pressing concerns for most people is the cost of energy: how much am I paying for my energy usage and how can I become more efficient?
This is not just motivated by concerns about global warming or pollution, it’s obviously a budgetary requirement – we simply can’t afford to waste energy. The difference between a householder and the petrochemical plant manager is just scale, though not necessarily proportionality.
Many large-scale manufacturers are very concerned about their energy usage, as making savings in that area will likely directly affect the profitability of the company. And finding ways to minimise the use of energy is increasingly a job for data analysts and, perhaps in the future, artificial intelligence systems.
For Honeywell UOP, too, energy saving is not only a concern, finding ways to reduce energy usage is central to its business, and it’s what motivates the company to file so many patents. Energy, after all, is unlikely to get any cheaper in the long run. And the light through our windows is not going to power our computers any time soon, neither is wind power going to blow enough heat through our radiators.
Peak word count
Honeywell is a diverse, industrial giant that operates in a number of different markets. Its petrochemicals customers include companies which operate dozens of plants in a wide range of locations. And as industry becomes more data-driven, the company could become a leading power within the computing world as well.
Everyone needs data, and they need it to be presented in a form that they can understand and act upon. Which is probably why Honeywell UOP launched its Connected Performance Services in the first place a couple of months ago.
As more and more people are acknowledging, data is the crude oil of the 21st century, and unlike oil production, which some say has reached its peak, data mining is in its very early days. And even though computerised data has already virtually taken over the world, there’s a lot more where that came from – always will be, whether we’re here to analyse it or not.
Related
Related Posts
-
37
Honeywell says a subsidiary of PetroVietnam will use its new IIoT-based Connected Performance Services (CPS) offering to improve the performance of its manufacturing operations in Quang Ngai City, Vietnam. Binh Son Refining and Petrochemical (BSR) will use Honeywell’s CPS technology which integrates Honeywell UOP’s deep process knowledge to improve refinery…
Tags: honeywell, oil, plant, petrochemical, uop, data, gas, refinery, energy
-
33
General Electric has launched two new high-tech component production lines at the GE Oil & Gas plant in Talamona, Italy. A new nozzle production line is the first completely automated line for GE Oil & Gas, and a new additive manufacturing line will use laser technology to 3D print burners for…
Tags: gas, oil, manufacturing, production, plant
-
31
DeviceLynk has released a new user experience offering a completely redesigned interface focused on improving navigation and ease of use. The company says the new design brings a modern touch-centric concept to Industrial IoT, an industry merging the needs of Industrial Automation with the technology of the Internet of Things. The new DeviceLynk…
Tags: industrial, equipment, data, energy, company, industry, things, oil, gas